- Ultra-fine powder mill processes gypsum
- What kind of grinding mill is used for the production and processing of limestone powder?
- Ultra-fine powder mill processes metallic silicon
- The superfine powder mill processes fluorite
- Ultra-fine grinding mill processes talc
- Superfine grinding mill processes bauxite
Telephone:
+86-18290113988 (whatsapp) Kase
+86-13248239223 (whatsapp) Cecilia
+86-17317879223 (whatsapp) Fandi
+86-19921225405 (whatsapp) Luna
Email:sales@shcronus.com
Introduction and Maintenance of Raymond Mill Parts
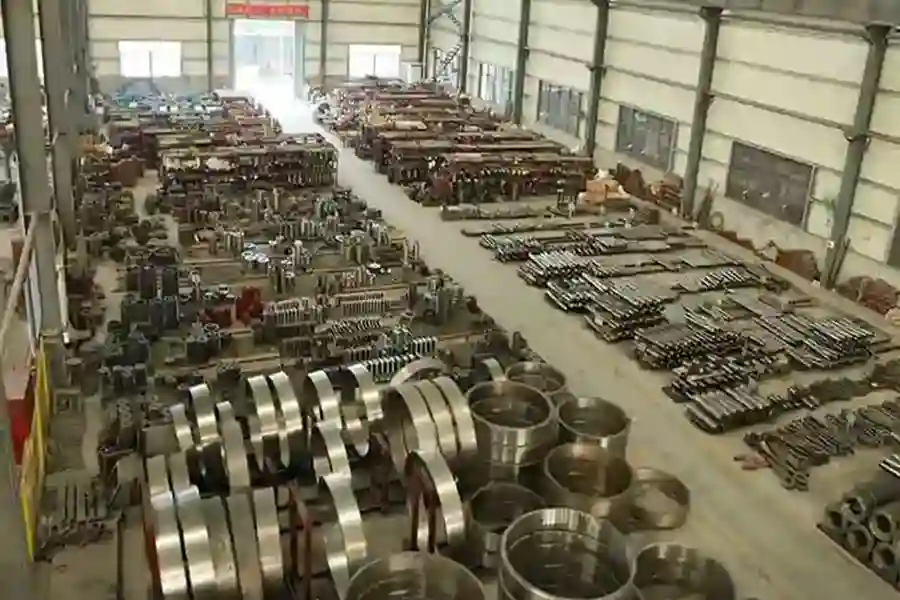
- Publication time:2025-07-03
- Click:32
Raymond mill can grind ores, chemical raw materials, etc. into fine powder, and plays a crucial role in industries such as mining, building materials, and chemical engineering. Its efficient and stable operation depends on the close cooperation of various parts.
Raymond mill parts: grinding rolls and grinding rings
Rollers and grinding rings are the grinding core of Raymond mill. The rollers and grinding rings cooperate closely to grind materials. There are 3 - 5 rollers, which are pressed against the grinding ring under the action of centrifugal force. The shovel blade feeds materials, and the rollers roll to crush the materials. The materials of the rollers are diverse. High manganese steel is wear - resistant and impact - resistant, and alloy steel has strong balance and toughness.
Daily maintenance: To ensure the efficient and stable operation of the Raymond mill, it is necessary to regularly check the wear of the rollers and grinding rings. If the wear exceeds 20% - 30%, they should be replaced in a timely manner. Regularly add high - temperature - resistant lubricating grease, such as lithium - based grease, to the roller bearings. When replacing, the rollers and grinding rings should be replaced in pairs. If necessary, use wear - resistant welding rods for surfacing repair.
When the Raymond mill is running, the feeding should be uniform to avoid the impact of large and hard materials, and the air volume should be adjusted reasonably. Problems such as roller pressure, overheating, and abnormal vibration should be dealt with in a timely manner.
Suggestions: Check the lubrication system and fasteners daily, clean the residual materials weekly, and conduct a comprehensive disassembly inspection every 3 - 6 months.
Raymond mill parts: plum blossom frame
The plum blossom frame supports the grinding roller, drives its revolution and rotation, and realizes efficient grinding. High-strength cast steel material is adopted. Its stability directly affects the operation efficiency and service life of the equipment.
Daily maintenance: Check for cracks, deformation, and welding points daily, ensure that the bolts are tightened, and regularly add molybdenum disulfide grease to the central bearing. Focus on monitoring the wear of the inner contact surface. If it exceeds 5mm, repair it by surfacing welding with electrodes, and perform balance correction after repair.
For the operation of the Raymond mill, maintain a uniform load and check for abnormal vibration. If there is a fracture, replace it with a high-strength material. If the bolts are loose, use anti-loosening washers. If the bearing overheats, replenish lubrication or replace it.
Suggestions: Check the bolts and vibration daily, check for wear and lubricate monthly, and conduct a comprehensive overhaul annually.
Raymond mill parts: shovel blade
The shovel blade scoops up the materials and sends them into the grinding area. It is made of wear-resistant alloy material. Wear affects the scooping ability and grinding effect.
Daily maintenance: As a core vulnerable part, the shovel blade needs to be inspected for wear every day. If the thickness reduction exceeds 1/3 or there is a chipping edge, it needs to be replaced. Ensure that the bolts are tightened and use 8.8 grade high-strength bolts. Maintain a clearance of 5 - 8mm with the grinding ring. The support bearings need to be filled with molybdenum disulfide grease every 300 hours. After wear, welding rods can be selected for repair welding. Preferentially replacing the high-chromium cast iron shovel blades in groups can extend the service life by 2 - 3 times.
Suggestions: The maintenance cycle is to check for wear every shift, tighten the bolts every week, and comprehensively replace them every 3 - 6 months. When the machine is stopped, the remaining materials need to be cleaned and keep 2 sets of spare parts in stock. Pay attention to the size differences of shovel blades of different models (3R/4R/5R). Confirm the equipment specifications before replacement.
Raymond mill parts: classifier
The classifier screens materials by particle size through rotating blades, controlling the fineness of the finished product between 80 - 325 meshes, and the rotation speed can be adjusted to meet different needs. Its key components include blades, rotors, and reduction motors.
Daily maintenance: Check the wear and clearance of the classifier blades. Use high - chromium cast iron material and replace them in groups. Regularly add molybdenum disulfide grease to the bearings. In daily operation, match the air volume with the feed volume to prevent overload and blockage. If the fineness is unstable, adjust the air volume and replace the blades. If the vibration is large, adjust the balance and replace the bearings.
Suggestions: Check the blades every week, lubricate the bearings every 500 hours, replace the worn parts during the annual inspection, stop the machine to clean the accumulated powder and record the data. Give priority to using original factory accessories. Maintaining balance accuracy can extend the service life.
Raymond mill parts: reducer
The motor provides power. The reducer converts the power of the motor into power suitable for the Raymond mill.
Daily maintenance: The gear oil for the reducer should be selected strictly according to the season. Change the oil for the first time after 300 hours of operation, and then change it every 2,500 hours or half a year.
Suggestions: Check the oil level every week. After the machine stops for 5 minutes, the oil level should be at 1/2 to 2/3 of the sight glass. Monitor the bearing temperature (≤75℃) and vibration value (≤2.8mm/s). If oil leakage is found, immediately replace the fluororubber oil seal. If gear pitting occurs, change the oil or repair the tooth surface. If the shaft vibrates, check the alignment and bearings. Disassemble and inspect the gears and bearings (clearance ≤0.2mm) every year, and establish a regular oil testing system.
Raymond mill prats: drive belt
The transmission belt directly affects the stability and efficiency of the Raymond mill's operation.
Daily maintenance: The tension of the transmission belt should be checked daily. It is advisable that when pressed, the depression is 10 - 15mm. Check for wear. If there are cracks or the side wear exceeds 3mm, replace it immediately. Ensure that the misalignment of the pulley is ≤1mm/m. When replacing, it must be carried out synchronously in groups. Select belts of the original factory specifications. Installing a protective cover to prevent dust and avoiding contact with oil and water can significantly extend the service life.
Suggestions: Replace preventively every 6 - 12 months, and keep 1 - 2 sets of spare belts on hand.
Summary
The components of the Raymond mill work in coordination. Regular maintenance and timely replacement of components are crucial. Cronus grinding equipment manufacturer provides high - quality grinding mill parts.
- Previous:How to extend the service life of the Raymond mill
- Last:Analysis of Limestone Powder Process, Application and Indica···
向下滚动页面显示"置顶"按钮...