- Ultrafine grinding mill processing coke
- Ultrafine grinding mill processing graphite
- Ultrafine grinding mill processing gangue
- Ultra-fine powder mill processes gypsum
- What kind of grinding mill is used for the production and processing of limestone powder?
- Ultra-fine powder mill processes metallic silicon
Telephone:
+86-18290113988 (whatsapp) Kase
+86-13248239223 (whatsapp) Cecilia
+86-17317879223 (whatsapp) Fandi
+86-19921225405 (whatsapp) Luna
Email:sales@shcronus.com
Calcite powder production process
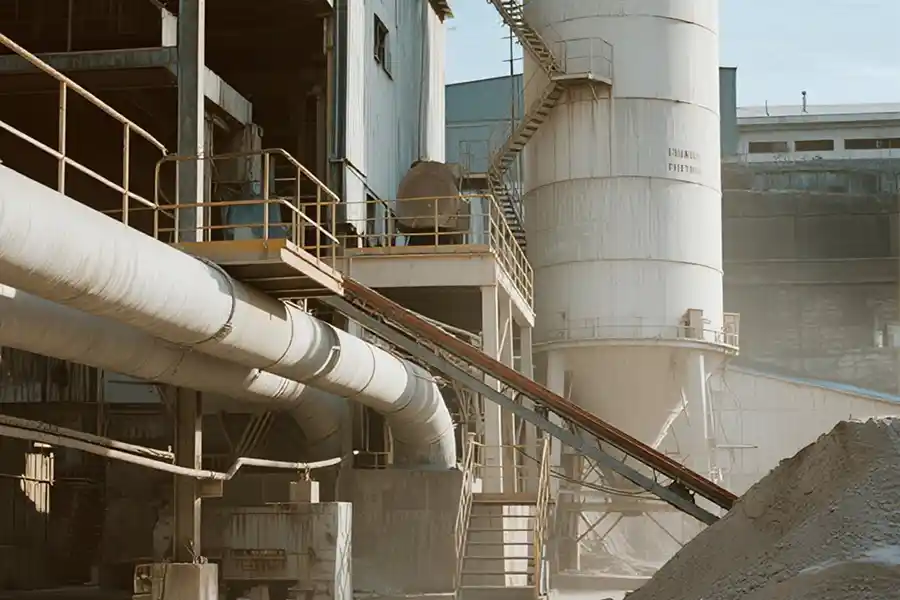
- Publication time:2025-07-09
- Click:26
What is calcite powder?
Calcite powder is an important industrial raw material. It is a powdery product made from the natural mineral calcite (with a chemical composition of calcium carbonate, CaCO₃) through processing techniques such as crushing, grinding, and classification.
The mining process of calcite
Raw material mining: Calcite is mainly found in deposits such as limestone and marble. Geological exploration is carried out before mining, and the mining methods include open - pit and underground mining.
The coarse - crushing stage: It is mainly completed by jaw crushers and hammer crushers, crushing the ore to ≤5cm.
The dry production process of calcite powder
The medium - crushing process: Impact crushers and cone crushers are the main equipment. Impact crushers have a large crushing ratio and high efficiency, and can crush materials to ≤1cm; cone crushers have a strong crushing force, and the product has a uniform particle size and good particle shape.
Dry grinding: Raymond mills have low energy consumption and high production capacity, and are suitable for producing ordinary powders of 80 - 400 mesh; the combination of ball mills and classifiers is good at producing fine powders of 400 - 1500 mesh and can accurately control the particle size.
Classification: Cyclone separators and turbine classifiers complete the classification, and turbine classifiers have high precision.
Iron removal: Magnetic separators are the main equipment for iron removal, which can improve the whiteness and purity of calcite powder.
Storage: The finished products are packaged in ton bags or small bags and should be stored in a dry and well - ventilated warehouse with the humidity controlled at ≤60%.
The wet production process of calcite powder
Wet grinding: Stirred mills and sand mills are the main equipment, suitable for preparing ultra - fine powders of 1500 - 6000 mesh. Dispersants can improve the grinding efficiency.
Classification: Hydrocyclones and centrifugal classifiers complete the classification.
Dehydration: Filter presses and centrifuges are the main dehydration equipment.
Drying: Spray drying towers and flash dryers are used for drying.
Surface modification: Spray drying towers and flash dryers are used for drying; dry - type modification and wet - type modification can improve the application performance of calcite powder.
Ultra - fine classification: Airflow classifiers can accurately control the final particle size of calcite powder to meet the requirements of high - end fields.
The surface modification process of calcite powder
Performance improvement: Reducing the oil absorption value of the powder, reducing the amount of resin used; enhancing the compatibility with organic materials and improving the performance of composite materials.
Common modifiers: Stearic acid is used in the plastics and rubber industries; titanate is a useful assistant in the coating field; silane is often used for the modification of composite materials.
The selection of the production process of calcite powder
Dry process: The fineness range is 80 - 1500 mesh, with low cost, high production capacity, and a simple process, but there is a lot of dust and the lower limit of the particle size is limited. It is suitable for industries such as plastics and coatings.
Wet process: The fineness range is 1500 - 6000 mesh, with high product quality, less dust pollution, but high cost, high energy consumption, and a complex process. It is suitable for high - end industries such as high - end papermaking, medicine, and cosmetics.
Summary
The production process of calcite powder is divided into dry method and wet method. The dry method has low cost and high output, but generates a lot of dust, making it suitable for mid - to - low - end fields. The wet method has high purity and uniform particle size, but has high costs and energy consumption, making it suitable for high - end industries.
- Previous:The Function and Maintenance of Raymond Mill Shovel Knife
- Last:How to extend the service life of the Raymond mill
向下滚动页面显示"置顶"按钮...