- Raymond mill processes white carbon black
- The CR5R4128 Raymond Mill is loaded onto the vehicle and shipped
- The Function and Maintenance of Raymond Mill Shovel Knife
- Calcite powder production process
- How to extend the service life of the Raymond mill
- Raymond mill supporting equipment: bucket elevator
Telephone:
+86-18290113988 (whatsapp) Kase
+86-13248239223 (whatsapp) Cecilia
+86-17317879223 (whatsapp) Fandi
+86-19921225405 (whatsapp) Luna
Email:sales@shcronus.com
Raymond mill processes white carbon black
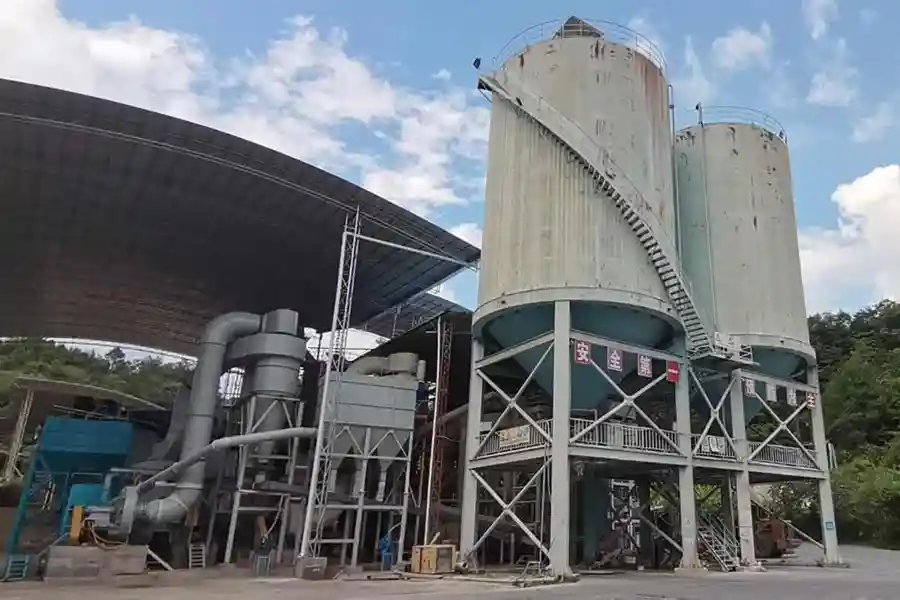
- Publication time:2025-07-24
- Click:4
What is precipitated silica?
Precipitated silica (amorphous silica nanomaterial with the chemical formula SiO₂・nH₂O) is a key material widely used in fields such as automotive tires, cosmetics, coatings, and electronic packaging materials. In terms of preparation methods, precipitated silica made by the precipitation method has a low cost and is used in general industries. Fumed silica has high purity and excellent performance but a high cost, so it is used in high - end fields. Precipitated silica has unique physical properties, such as a large specific surface area, high porosity, low density, good insulation, and stable chemical properties. The surface silanol groups can be modified to expand its applications.
The Processing Technology of Precipitated Silica by Raymond Mill
The Mohs hardness of precipitated silica is 6 - 7, which is within the applicable range of the Raymond mill. It is suitable for medium - capacity demands, with a processing capacity of 0.5 - 20 tons per hour and relatively low energy consumption. Precipitated silica has a strong agglomeration property, a large specific surface area, and is prone to adsorb moisture and generate static electricity, which affects the grinding efficiency and the fluidity of the finished product. Silicon dioxide significantly wears the grinding rollers and rings. Traditional Raymond mills are difficult to directly achieve nano - level fineness. To produce high - end products, other equipment or processes need to be combined, increasing costs.
Feed Particle Size: It is recommended to be ≤20mm. If it is too large, it is easy to cause blockage and overload. If it is too small, it will increase the pretreatment cost and time. It needs to be pre - crushed to an appropriate particle size by a crusher.
Drying: The raw materials of precipitated silica need to be dried until the moisture content is ≤2%, to prevent agglomeration and adhesion to the equipment.
Grinding Roller Pressure: It is recommended to be 0.8 - 1.2MPa. If the pressure is too low, the fineness will be insufficient. If it is too high, the precipitated silica will heat up, changing its chemical structure and affecting its application performance. It needs to be precisely adjusted according to its characteristics and fineness requirements.
Classifier Rotation Speed: The rotation speed range is 80 - 200rpm. The higher the rotation speed, the finer the screening. It needs to be adjusted according to the fineness requirements. If the rotation speed is too low, it will affect the product quality.
Air Volume: It is recommended to be 15 - 25m³/min. An appropriate air volume ensures transportation, avoids the escape of fine powder or system blockage. Both too large and too small air volumes will affect the grinding efficiency and product quality.
Temperature Control: It needs to be controlled at ≤60℃. High temperatures will damage the surface structure, affecting the chemical activity and physical properties. An air - cooling or water - cooling system is required.
Processing precipitated silica by the precipitation method can improve the particle uniformity, enhance the filling performance, strengthen the strength and wear resistance of rubber, and improve the mechanical properties and transparency of plastics. Over - grinding will cause the specific surface area to decrease, the pore structure to be damaged, and reduce the adsorption capacity and physical properties. The mechanochemical effect activates the silanol groups, affecting the subsequent modification effect. Producers need to strictly control the process parameters and consider the impact of processing.
Key Points of Processing Precipitated Silica by Raymond Mill
Material of Core Components: The grinding rollers and rings are selected from high - chromium cast iron (Rockwell hardness HRC≥58) or tungsten carbide - coated materials. The shovel is made of manganese steel or wear - resistant alloy to resist the wear of silicon dioxide.
Anti - agglomeration Measures: Introduce an air - flow dispersion device, such as a compressed - air nozzle, into the grinding chamber or classifier. Add a small amount of grinding aids, such as calcium stearate (with an addition amount of 0.1% - 0.5%), but the impact on product quality needs to be considered.
Dust Removal System: Equip a pulse - jet bag dust collector to effectively collect fine powder, prevent pollution, recycle resources, and meet environmental protection requirements.
Safety Protection: Fine powder of precipitated silica has an explosion risk. The operation room should be grounded for anti - static, explosion - proof equipment should be selected, operators should wear anti - static clothing, fire - fighting facilities should be equipped, and regular drills should be carried out.
Summary
When processing white carbon black with a Raymond mill, it is necessary to precisely control the process parameters and pay attention to key aspects such as the wear resistance of core components, anti - agglomeration, dust removal and environmental protection, as well as safety protection.
向下滚动页面显示"置顶"按钮...