- Raymond mill processes white carbon black
- The CR5R4128 Raymond Mill is loaded onto the vehicle and shipped
- The Function and Maintenance of Raymond Mill Shovel Knife
- Calcite powder production process
- How to extend the service life of the Raymond mill
- Raymond mill supporting equipment: bucket elevator
Telephone:
+86-18290113988 (whatsapp) Kase
+86-13248239223 (whatsapp) Cecilia
+86-17317879223 (whatsapp) Fandi
+86-19921225405 (whatsapp) Luna
Email:sales@shcronus.com
雷蒙磨加工碳化硅
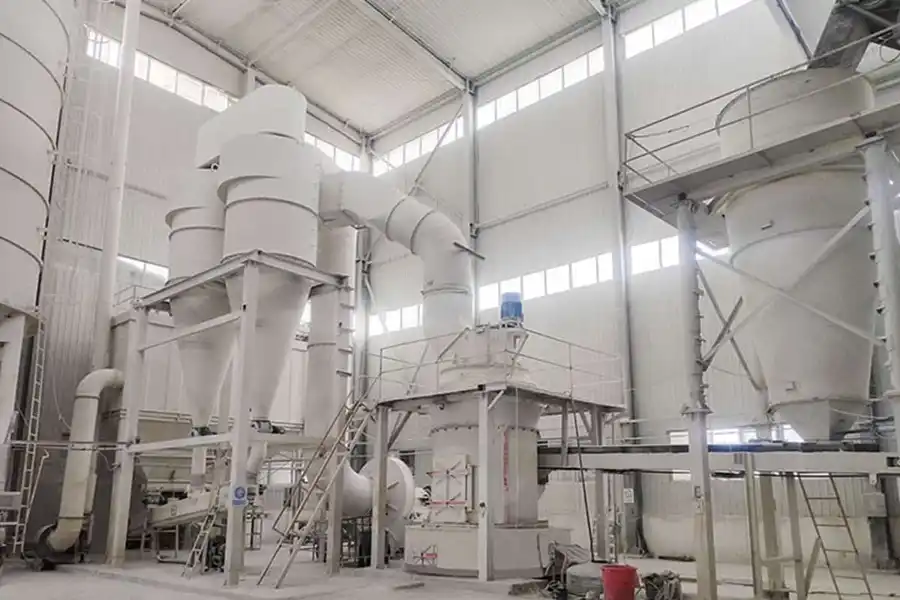
- Publication time:2025-07-25
- Click:0
Raymond Mill and Silicon Carbide
Silicon carbide (SiC) is a compound formed by silicon (Si) and carbon (C). It belongs to wide bandgap semiconductor materials with a bandgap of approximately 3.2 eV, three times that of silicon. It can operate stably under high temperature, high pressure, and high frequency with low conductive loss.
The Raymond mill processes silicon carbide to produce powders with a fineness of 80 - 400 mesh. The system integrates a classification function and can adjust the fineness as required. However, the hardness of silicon carbide is close to the limit of the Raymond mill. During processing, the core components need to be strengthened. High - chromium alloys (such as Cr20Mo2Cu) can be selected for the grinding rollers and grinding rings, or tungsten carbide (WC) coatings can be applied to improve wear resistance. The classification impeller uses cemented carbide blades to reduce wear. In terms of parameter control, the spindle speed should be appropriately reduced (e.g., controlled at 80 - 100 rpm) to balance efficiency and grinding. Increase the air volume of the fan to prevent fine powder from adhering.
Applications of Raymond Mill Processing Silicon Carbide
Polishing Field: Silicon carbide micropowder is a high - quality polishing material. The 200 - 325 mesh micropowder processed by the Raymond mill can be used for mobile phone screen polishing to improve product quality.
Ceramic Additive Field: It can improve the performance of ceramics. The Raymond mill can produce micropowder with uniform particle size, providing a raw material guarantee for ceramic additives.
Wear - resistant Coating Field: It is an important component to enhance the wear resistance of coatings. The micropowder processed by the Raymond mill can be evenly dispersed in the coating to improve wear resistance.
Process of Raymond Mill Processing Silicon Carbide
Feed Control: Pre - crush the raw materials and control the particle size to ≤5mm to reduce the load on the mill. Use a quantitative feeding device to feed evenly to prevent blockage or empty grinding.
Classification Adjustment: Control the target fineness at 200 - 325 mesh (D50 = 20 - 50μm), and control the particle size by adjusting the rotational speed of the analyzer.
Cooling and Temperature Reduction: Install a cooling system (such as a water - cooling device) and monitor the bearing temperature in real - time.
Semiconductor - grade Pretreatment: The Raymond mill plays an important role in the coarse - crushing stage of semiconductor - grade SiC pretreatment. It can initially crush the bulk raw materials into an appropriate particle size, reducing the load on subsequent processing equipment and improving overall efficiency. The particles processed by it have a uniform particle size and a large specific surface area, which is conducive to acid - washing and purification to obtain high - purity materials, providing support for semiconductor device manufacturing.
Protection Measures: Silicon carbide dust is explosive. A pulse dust collector needs to be equipped, and high - pressure gas pulse technology is used to collect dust to reduce the explosion hazard. Install an anti - static device, ground the equipment housing, pipelines, etc., use anti - static dust - collecting bags, and workers should wear anti - static equipment to prevent explosions caused by static electricity.
Summarize
Through wear-resistant optimizations such as high-chromium alloy grinding rollers and tungsten carbide coatings in the processing of silicon carbide, the Raymond mill can stably produce 80 - 400 mesh powder, meeting the demands of polishing, ceramics, coatings, etc.
- Previous:没有了!
- Last:Raymond grinding mill processes fluorite
向下滚动页面显示"置顶"按钮...