- Raymond mill processing of metallic silicon
- Raymond mill processes white carbon black
- The CR5R4128 Raymond Mill is loaded onto the vehicle and shipped
- The Function and Maintenance of Raymond Mill Shovel Knife
- Calcite powder production process
- How to extend the service life of the Raymond mill
Telephone:
+86-18290113988 (whatsapp) Kase
+86-13248239223 (whatsapp) Cecilia
+86-17317879223 (whatsapp) Fandi
+86-19921225405 (whatsapp) Luna
Email:sales@shcronus.com
Raymond mill processing of metallic silicon
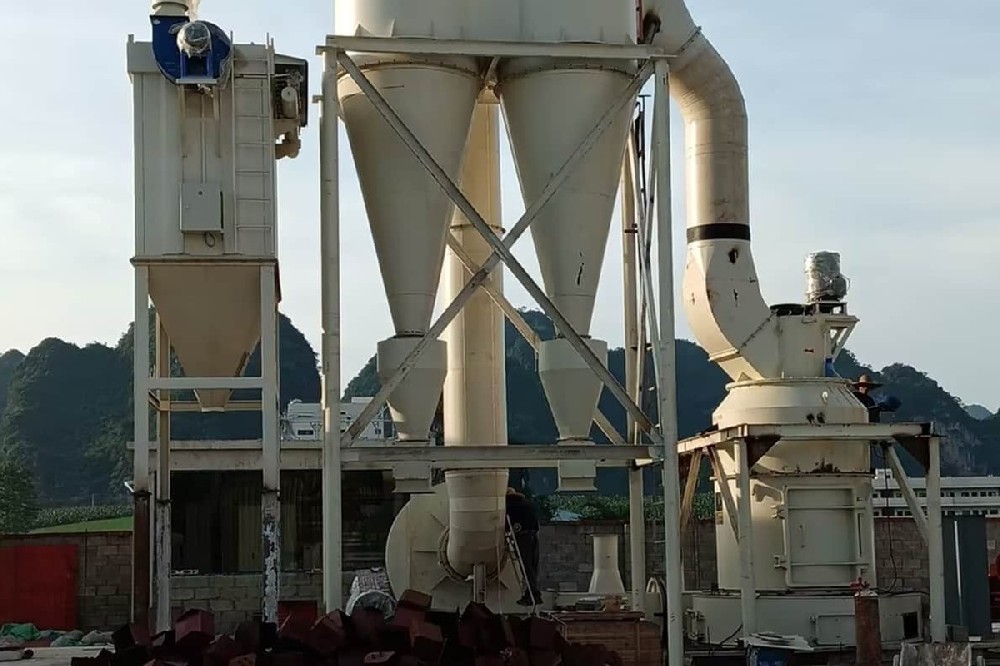
- Publication time:2025-07-28
- Click:0
What is metallic silicon?
The chemical symbol of metallic silicon is Si, with an atomic number of 14, a melting point of 1414°C, a boiling point of 3265°C, and a density of 2.33 g/cm³. Its chemical properties are stable at room temperature, and it is resistant to acids (except hydrofluoric acid). At high temperatures, it reacts with oxygen, halogens, etc., and has semiconductor properties. It is a key material in the electronics industry. According to purity, metallurgical-grade silicon (95% - 99%) is used in the fields of aluminum alloys and organosilicon; chemical-grade silicon (above 99%) is the raw material for producing silane and polysilicon; electronic-grade silicon (above 99.9999%) is used to manufacture semiconductor chips and solar cells.
The process of processing metallic silicon with Raymond mill
Coarse crushing: Use a jaw crusher to crush metallic silicon blocks to ≤30mm to prepare for powder grinding.
Drying (optional): If the raw material is damp, use drying equipment to reduce the moisture content to <1% to prevent affecting the powder grinding efficiency and product quality.
Powder grinding: The metallic silicon material enters the main unit of the Raymond mill. The grinding roller rolls and grinds, and the air flow of the fan transports it to the classifier. The qualified fine powder is separated, and the coarse powder returns to the main unit for re-grinding.
Collection: The qualified fine powder enters the pulse dust collector for collection. Before packaging, strictly test indicators such as iron content and particle size.
Key parameters: The feed particle size is ≤30mm; adjust the mill pressure according to the hardness of metallic silicon and requirements; adjust the air volume and wind speed through the fan; the fineness of metallurgical-grade silicon products is 80 - 200 mesh, and that of photovoltaic-grade silicon is 325 - 1000 mesh.
Key points of processing metallic silicon with Raymond mill
Fast equipment wear: The Mohs hardness of metallic silicon is 6.5 - 7, and ordinary grinding rollers and grinding rings are prone to wear. The grinding rollers and grinding rings of the Raymond mill are coated with high-chromium alloy or tungsten carbide, and the blades of the classifier are made of ceramic or hardened steel to extend the service life.
Flammable powder: The fine powder of metallic silicon is flammable. The Raymond mill is equipped with a nitrogen protection system, and an electrostatic elimination device and a spark detector are added to ensure production safety.
Iron pollution: Install a magnetic separator at the feed inlet, and strictly select the components in contact with the material to ensure the purity of high-purity products such as photovoltaic-grade silicon.
Finished product inspection: For metallic silicon products, especially photovoltaic-grade silicon, strictly test the impurity content to ensure that the quality meets the requirements.
Advantages of processing metallic silicon with Raymond mill
Raymond mill: It has a high cost-performance ratio in the medium-fineness (80 - 400 mesh) powder grinding field, has a simple structure, is convenient for operation and maintenance, and has a low equipment cost. However, it needs to be modified for explosion protection and has limitations in processing higher fineness.
Jet mill: It has a strong ability to produce ultra-fine powder (>800 mesh), the finished product has a uniform particle size distribution and regular particle shape, but it has high energy consumption, high operating costs, and high requirements for the gas source, and is suitable for high-end fields.
Ball mill + classifier: It is suitable for large-scale production, has a strong production capacity, and can accurately classify, but it covers a large area, has a high equipment investment, high noise, large wear, high maintenance costs, and may introduce impurities.
Conclusion
The Cronus Raymond mill, with its advantages of high-efficiency grinding, low cost, and explosion protection, has become the first choice for processing metallurgical/chemical-grade silicon powder. During production, it is necessary to accurately select the model according to the application (such as aluminum alloy, semiconductor, photovoltaic), optimize parameters, strictly control pollution and safety risks, and ensure high-quality and high-efficiency production.
- Previous:没有了!
- Last:Raymond mill processes white carbon black
向下滚动页面显示"置顶"按钮...